Track our transformation
Transparent insight into our processes
We’re in the middle of a transformation process. By 2030 we’re gradually moving away from all solvent -based lacquers and stains towards sustainable, alternative solutions. First and foremost, we see an eco-friendly future with aqueous products, but also with UV coatings, BRC coatings or natural oils . Many of our colleagues in Research & Development, from Product Management, but also from the Sales department are currently putting all their know-how into the development and testing of completely new coating systems. In addition to the pure formulation of a coating, the engineers in the Innovation Centre are shedding light on the entire coating process and looking for optimisation potential, such as in polishing or drying.
New developments are in principle the order of the day in the chemical industry. In the past we too have always brought new products involving optimisations to the market through close exchange with raw material manufacturers and internal development activities. But now everything is completely different. Our internal way of thinking and working has fundamentally changed. We’re exclusively focusing on sustainable and/or renewable raw materials and are forming small creative teams across departmental boundaries that pursue specific issues and develop solutions in a goal-based manner.
Here we’d like to give you a few insights into how and to what extent our laboratory colleagues are actively working on the development of new products.
The pore glows with PORECOLOR
Aqueous wiping stains impress all users
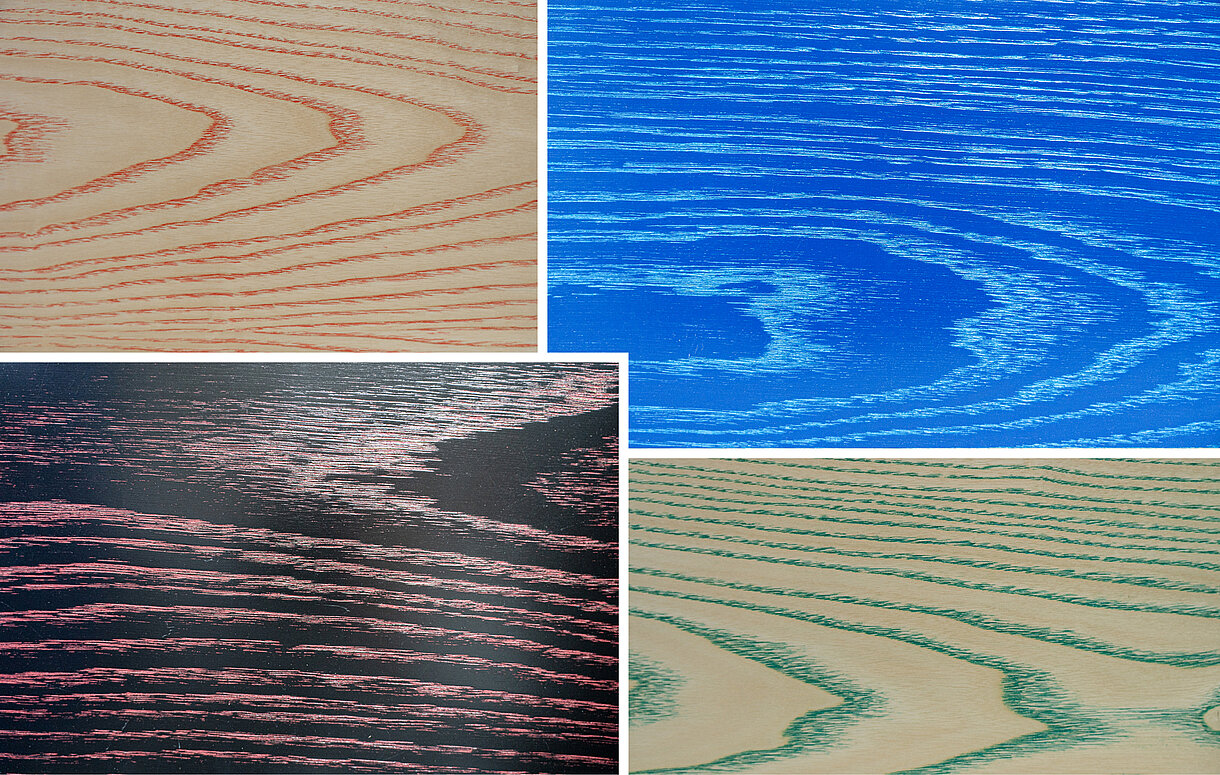
The pore glows with PORECOLOR
Aqueous wiping stains impress all users
The best replacement for traditional solvent-based wiping stains
Wiping stains always give the wood pore a very special look. Traditionally, wiping stains tend to be solvent -based. As part of our transformation, we have succeeded in developing a completely new water-based wiping stain. The goal was a wide range of colours, easy processing, good removal behaviour, a beautiful effect, universal finishing and miscibility via our stain mixing system.
Result
The newly developed wiping stain PORECOLOR has impressed all users! It was specially developed for open-pored or structured woods, is now available in many colour variants, and gives your project an individual touch. The application of PORECOLOR is very easy: the product can be applied with a brush, a pad, or a spray gun, and always guarantees a uniform result. In addition, the wiping stain can be easily overpainted with water-based paints.
Is HYDRO Metallic practicable?
Ambition is aroused in the creative team

Is HYDRO Metallic practicable?
Ambition is aroused in the creative team
Will CREATIVE-METALLIC be available as a water-based product in the future? Why shouldn’t this work? Numerous ideas and experiments have reached the practical phase.
In explanation: Metallic lacquers are highly valued by our customers. Real eye-catchers can be produced using their creative surfaces. And solvent -based CREATIVE-METALLIC is the most popular of all. This bulk product is as simple as can be. 112 metallic colour tones that are all mixable with each other and thus offer an unlimited variety of colours.
Our aim is to formulate just such a mass-market, simple water-based metallic lacquer. We do already have good aqueous metallic lacquers in our range, but they lag behind our solvent -based favourite in terms of quantity. We’re currently working on the unlimited HYDRO colour tone diversity. A small project team had interesting discussions at the European Coating Show and is working on the development of an adequate water-based metallic colour chart. The most important thing for us is to find the best metallic particles/pastes for formulation. Shelf life , practicality and variety are crucial. Expertise from the PU domain is very helpful and is used in a mutually profitable manner.
Outsmart the tannic acid with HYPERION
Oak stained white can be coated with HYDRO
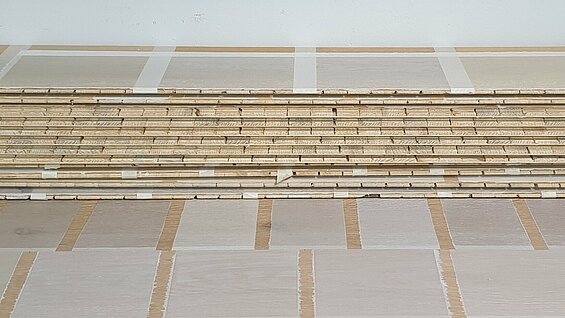
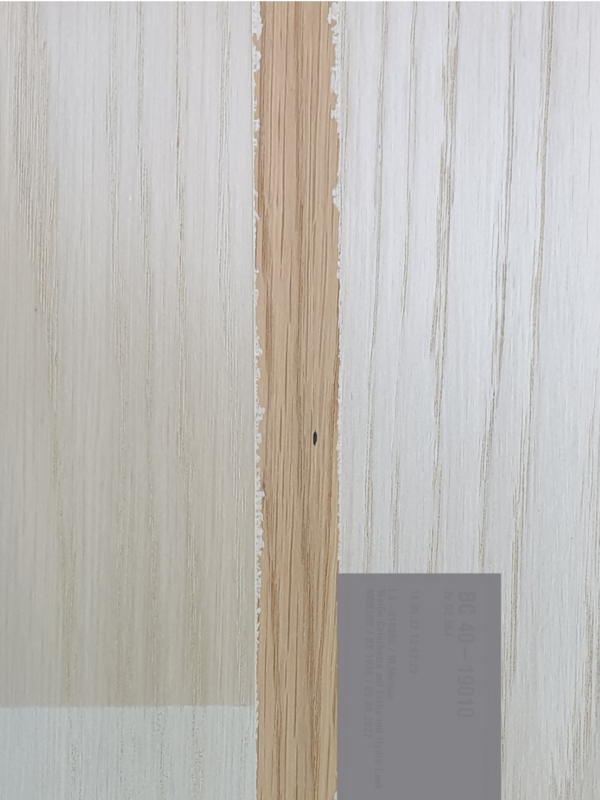
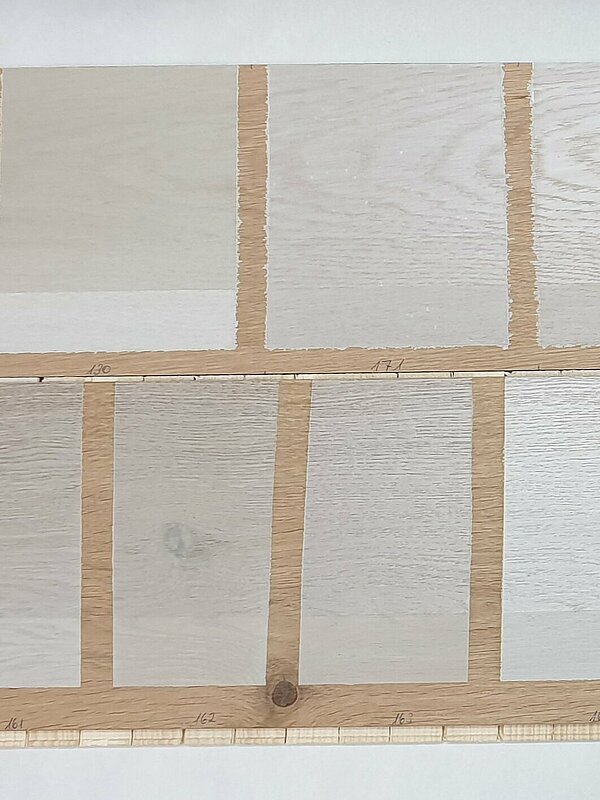
Outsmart the tannic acid with HYPERION
Oak stained white can be coated with HYDRO
We have the solution for you: HYPERION TI 130
The behaviour of oak stained white is not necessarily harmonious when it is coated with water-based varnish . As a wood expert, you know that tannic acid readily migrates out of the wood towards the stain, causing the surface to take on an unattractive green/brown discolouration. To ensure that the coating is still durable, this phenomenon has previously been circumvented using a solvent -based isolating layer – a batch that contradicts today's requirements for environmental friendliness.
With HYPERION TI 130, Hesse is now presenting an innovative solution that solves this problem in a sustainable way. The water-based insulation effectively blocks tannic acid and enables a completely water-based structure.
Insights into the development
The research and development behind HYPERION TI 130 was an intensive process. Numerous raw materials were tested in the laboratory, and the first results already showed promising batches. The extensive long-term tests in the climate cabinet now confirm the outstanding effectiveness and durability of the product.
The laboratory work includes hundreds of test surfaces that are meticulously documented – each step brought us closer to our goal: a sustainable, environmentally friendly solution for white-stained Oak using water-based coating systems.
The result
With HYPERION TI 130, we have not only succeeded in outwitting tannic acid, but also in controlling it in an environmentally friendly way. The surfaces remain bright white, without discolouration - even with demanding woods such as Oak. This marks a significant advance in wood finishing and underlines Hesse's claim to develop sustainable innovations for the highest quality standards.
Outlook
An exciting future
The suspense remains. We’re pursuing many other issues to attain a sustainable future, such as:
- What belongs to the field of renewable raw materials in the first place?
- Can recycled raw materials also be used effectively? If so, what does it all involve?
- What are the best hydro-based alternatives for high-solid alkyd enamels (primers, multicoat lacquers and top coats)?
- Will there also be a sustainable, water-based Zapon varnish in the future?
- and much more ...
As you can see, we’re actively working on our transformation. Together with our customers, we’re taking giant steps towards the future. Everyone who wants to be there is cordially invited to join us.
Success stories
How the transition is succeeding in practice
Stay up to date
with our newsletter
Your contact person
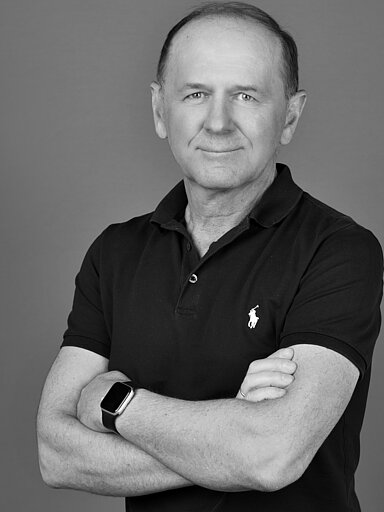
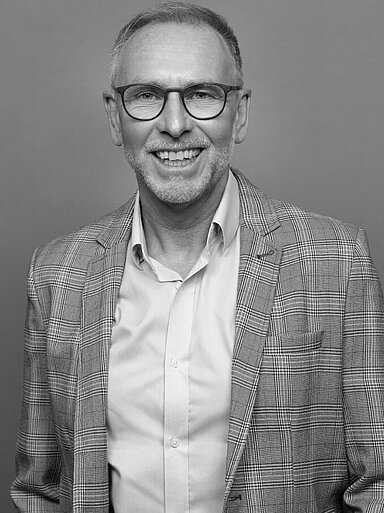