Versatile application options
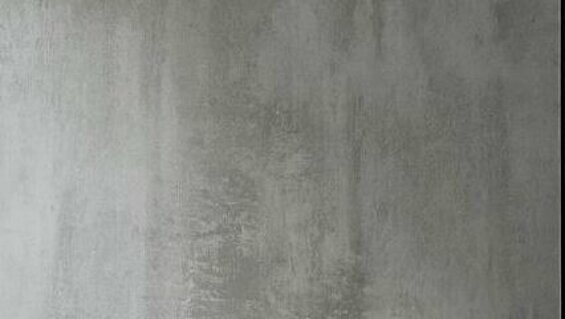
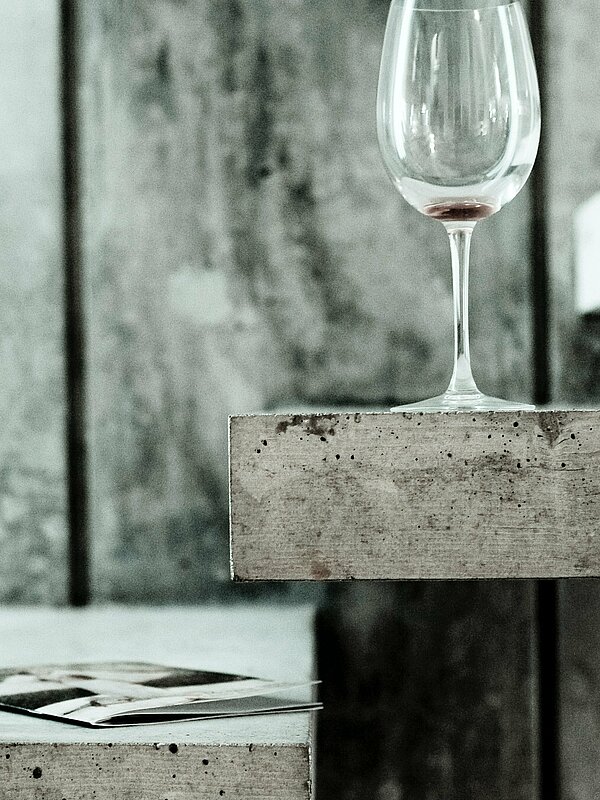
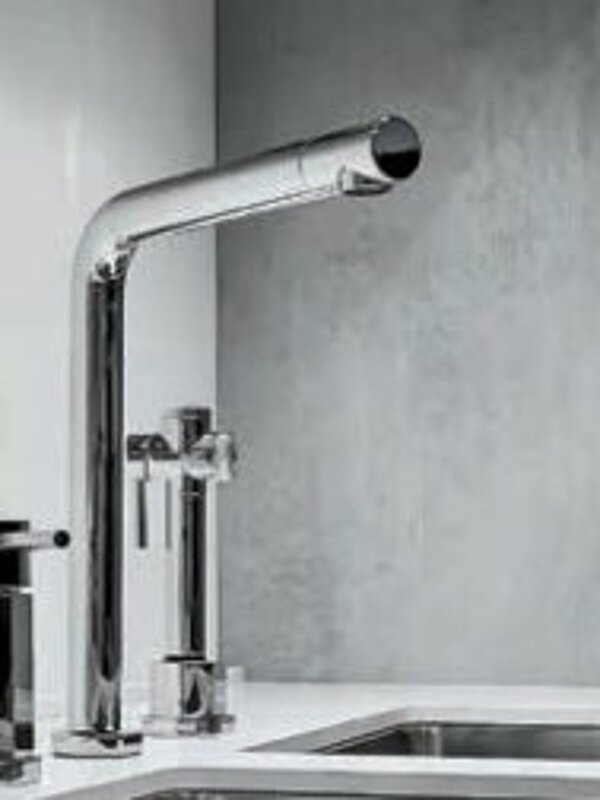
Versatile application options
Description/ features: this type of surface effect produces a concrete-look when the coating is applied. The special thing about this surface is that the effect can be applied to almost any substrate material imaginable and comes very close to the appearance of real concrete. The advantages of our Concrete effect are its quick and easy processing. In addition, this innovative effect is simple to achieve using standard Hesse products.
Fields of application : furniture and interior fittings.
How to achieve the Concrete effect
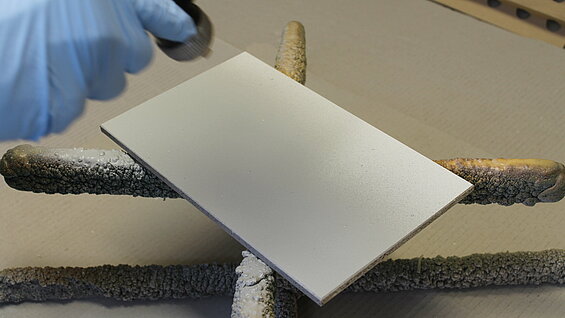
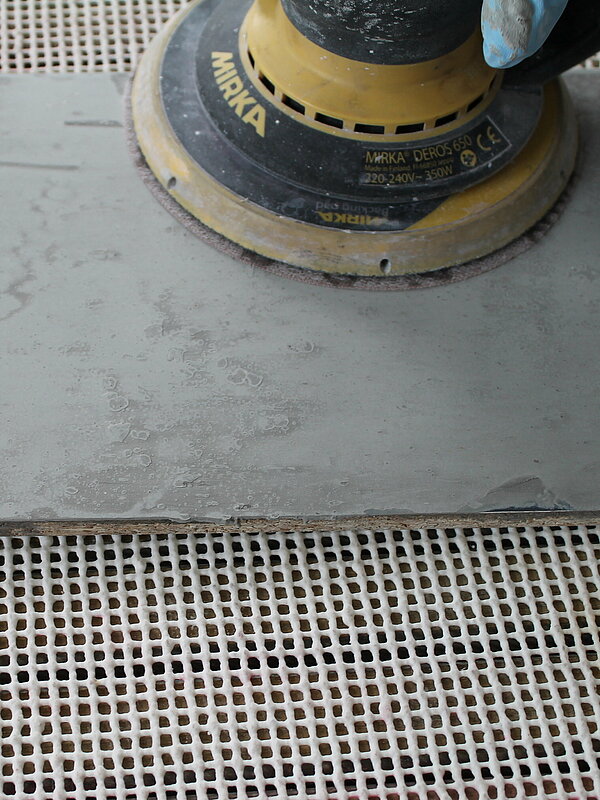
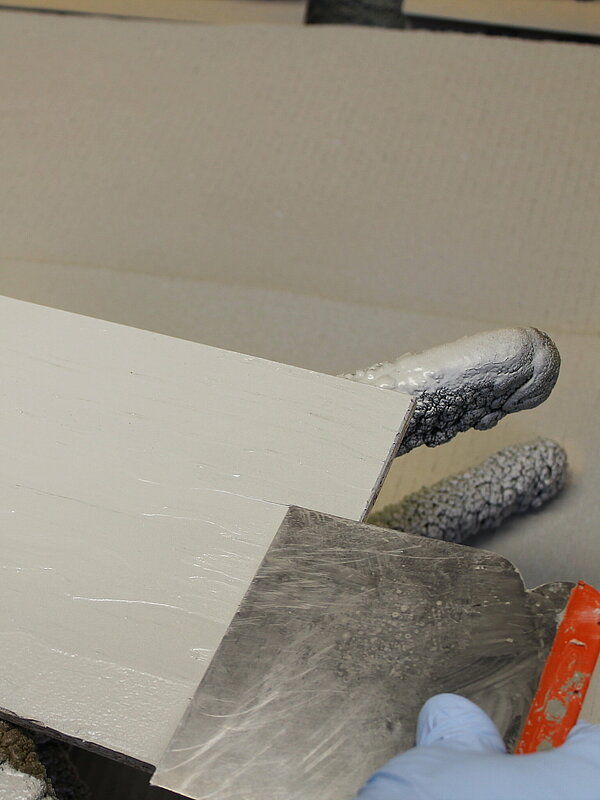
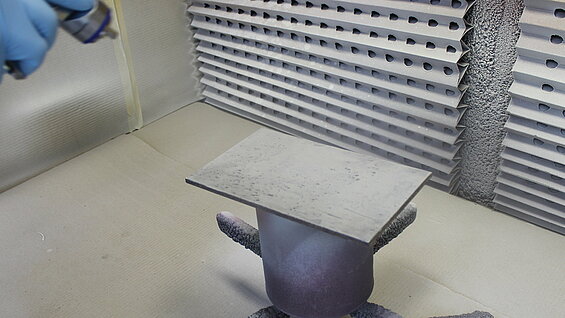
How to achieve the Concrete effect
Application example:
- make sure the chosen substrate materials (e.g. FPY or MDF with priming foil or melaminemastic foil) are well sanded. We recommend substrate sanding with 150 to 240 grit. If you are working with bare MDF surfaces or edges, then we recommend prior sealing with PU Isolating filler DP 4791-9343.
- Allow to dry for a minimum of 3 hours at 20 °C
- Then prime/prepare the substrate by spraying with one coat at 180 to 200 g/m². (Caution: you will need large spray nozzles). To do this you need to mix the following components from sealing filler, cement and hardener: PU Isolating filler DP 4791-9343 mixed 10 : 4 (by weight) with commercially available cement. You then need to blend this mixture evenly. Next you add the hardener to this filler/cement mixture at a mixing ratio (by volume) of 4 : 1 with PU Hardener DR 4058. As required, and depending on the part, you can add thinner of 10 to 15 % of PU Thinner DV 4900 to the filler/cement/hardener mixture.
- After a brief period of surface drying you can now create the actual concrete effect using a palette knife. You achieve the basic structure of the concrete-look with even, straight or individual swirling movements of the pallet knife. Although it is also possible to simply spray the sealing filler/cement mixture in order to retain an even concrete effect
- After drying for a minimum of 16 hours at 20 °C you can proceed with a surface or effect cutting back using 220 to 240 grit. You can also achieve whatever look you like by removing different layers when sanding (by hand, random orbital sander or sanding machine).
- You now evenly spray a light coat of Colour stain BC 85-22736 to obtain the typical concrete shade. Next follows wiping to achieve that distinctive patina (e.g. with a gauze ball or sponge).
- After around 2 hours at 20 °C a final coating is required with UNA-PUR DE 4259x(gloss level) at the desired gloss level. This can use the normal mixing ratio (by volume) of 10 : 1 with PU Hardener DR 4070.
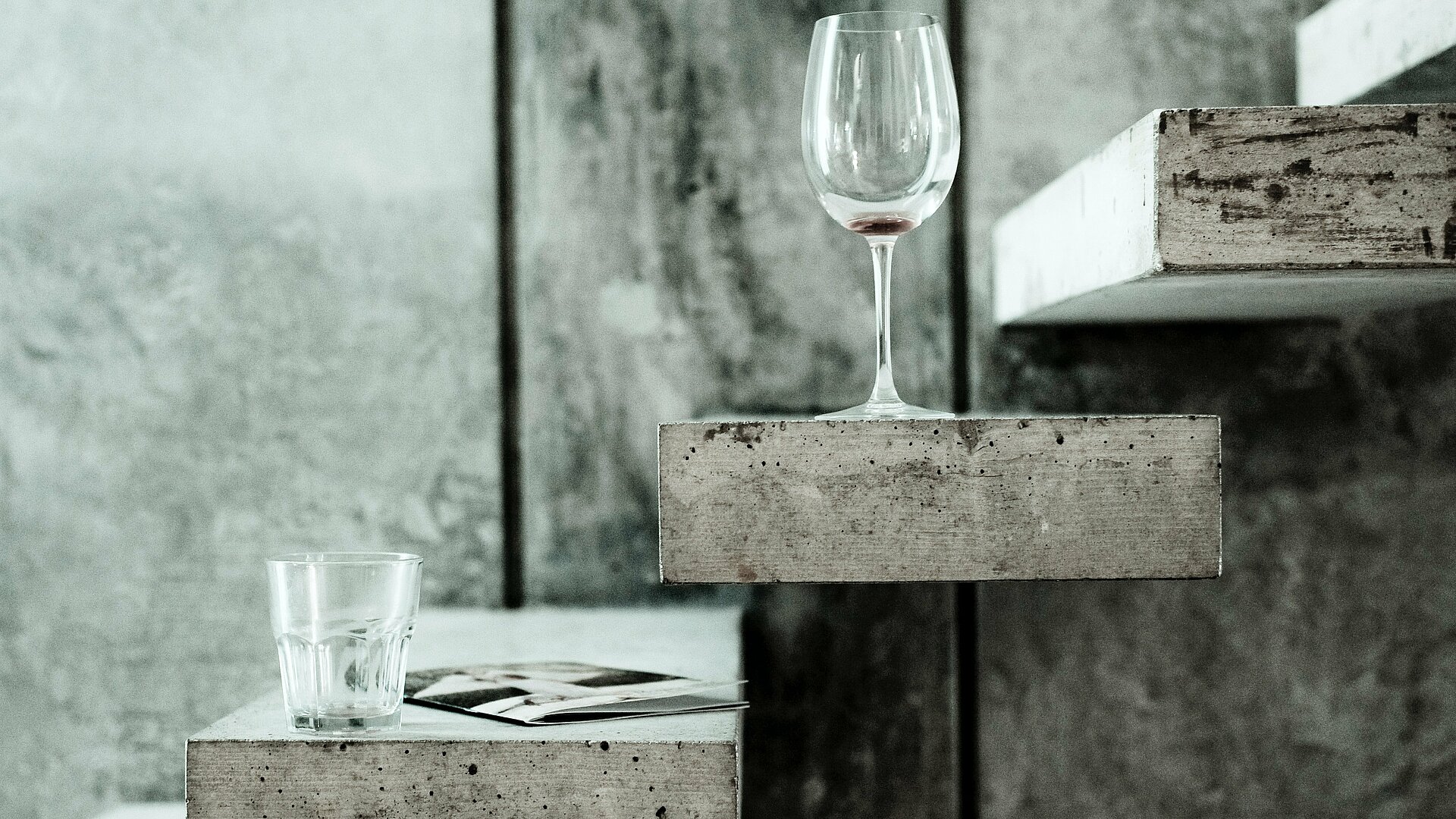
Technical information Concrete effect
Products required
Please observe the latest technical information and the material safety data sheets for the stated individual products. Particular instructions: PU lacquers should not be processed and dried at material and room temperatures below 18 °C. PU lacquered surfaces should be freshly sanded before finishing to avoid adhesion problems.
Warning: Please observe the precise addition of hardeners and thinners in the information below.
NoteThis information is purely advisory and is based on the best knowledge available after careful research in line with current state of the art technology. It is not legally binding. We also refer you to our Terms and Conditions. The material safety data sheet according to regulation (EC) No. 1907/2006 is available on request.
Contact partner
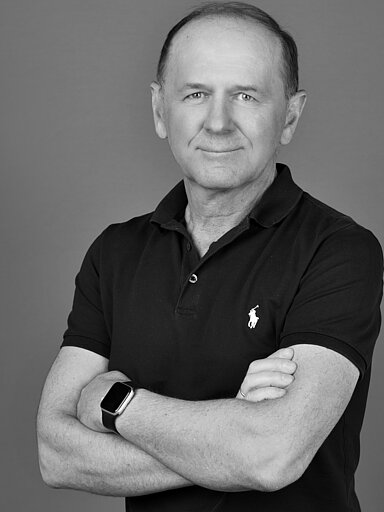