Versatile application options
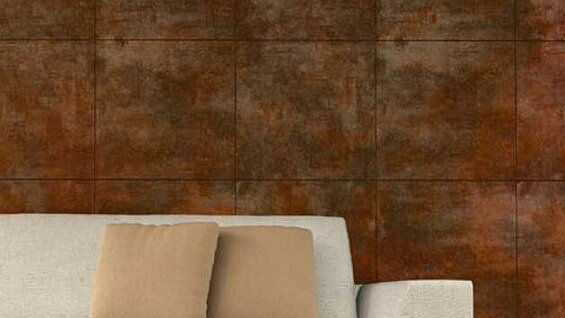
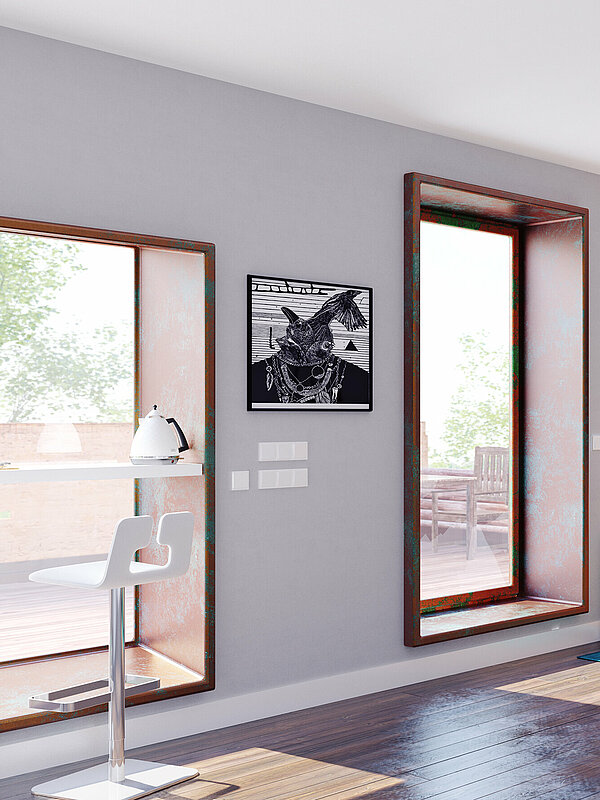
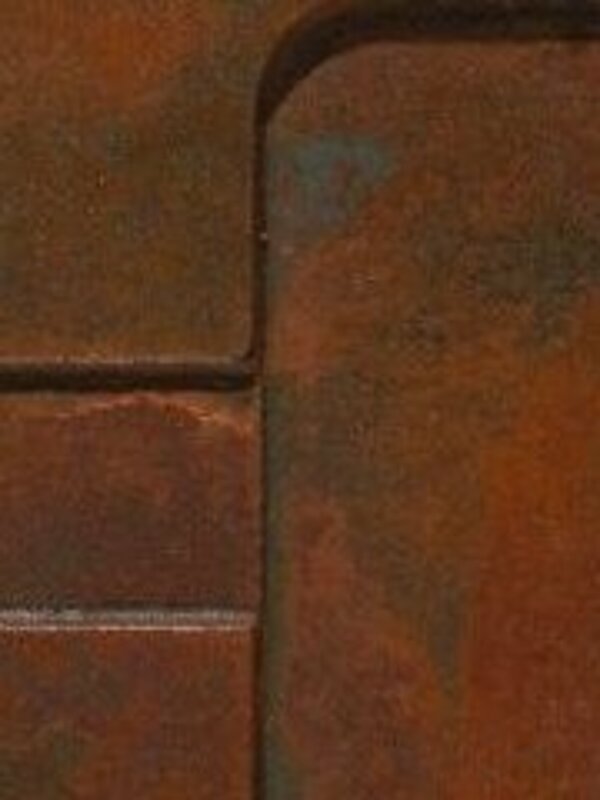
Versatile application options
Description: This method involves using HYDRO materials to simulate a rusting metal surface. No metal powder is required. The effect is influenced by the working method and can be created on all substrate materials on which HYDRO Pigment fillers or respectively HYDRO Colour lacquers can be used. The look can be appropriately varied by adopting various creative working methods. So every surface becomes a high quality, innovative and individual piece.
Fields of application : High-quality furniture and interior fittings, trade fair and shop fittings, kitchen and bathroom furniture.
How to – HYDRO rust effect
Practical suggestions:
- Sand the substrate material as appropriate (180 - 240 grit sandpaper).
- The HYDRO Pigment filler is either dyed with HYDRO colour concentrate "Basis" HF 21418 or individually with other HFM colour concentrates in the desired shade.
Added quantity:
- for 1C pigment fillers: 15 %
- for 2C pigment fillers: 20 % - The colour concentrate is stirred homogeneously by hand with a stirring rod or similar.
- Afterwards, 2 % of the HYDRO Filler additive HZ 74 is added and also intensively stirred by hand.
- 2C pigment fillers are now properly hardened and the hardener is thoroughly incorporated.
- 150 - 250 g/m2 of the accordingly modified pigment filler is then rolled onto the surface with the lacquer roller to accentuate the desired effect.
- Dry for at least 16 hours, maximum 48 hours at 20 °C room temperature.
- No lacquer sanding is necessary.
(A light amount of sanding with 400 - 600 grit paper or a fine sanding fleece need only be carried out with a drying time of more than 48 hours. Afterwards, thoroughly remove the sanding dust.) - HYDRO Filler Additive HZ 74 is added to the Hesse PERFECT-NATURA HDE 54500 and homogeneously stirred in by hand.
- Then this mixture is dyed with 10 % of the colour concentrate "Rust" HF 8008 and mixed well.
- This mixture is now hardened mixing ratio (by volume) 10 : 1 with HYDRO Hardener HDR 5091 at a ratio of.
- If desired, an additional 10 % of the effect booster HZ 76 can be added while stirring; it must be incorporated well after the hardener has been mixed in homogenously.
- This mixture is then rolled onto the existing pigment filling surface in a timely manner using the roller. It is ideally uneven and accentuated in order to imitate partial rust formation.
- The application quantity is between 80 and 120 g/m2
- If creating surfaces that will experience significant stress, an additional colourless protective layer of PERFECT-NATURA HDE 54500, optionally with PERFECT-TOP HDE 54000, mixing ratio (by volume) 10 : 1 with HYDRO Hardener HDR 5091, can be added. The lacquer can be applied with a roller or cup gun. Application quantity: 80 - 100 g/m2 .
- Dry for at least 16 hours at 20 °C room temperature.
- The surface will have reached its final resistance at about 7 days at 20 °C room temperature.
Hints and tips for creative effects:
- The mixture should be thoroughly stirred after the effect booster is added. For larger application quantities or larger surfaces to be lacquered, the lacquer mixture should be stirred at regular intervals in order to guarantee proper effect formation!
- Sand the selected substrate material well (e.g. FPY or MDF priming foil or melamine-mastic foil). We recommend sanding with 150 - 240 grit.
- We recommend filling raw MDF edges accordingly in advance in order to achieve a homogenous surface.
- The type and intensity of the surface obtained in the rust effect is originally determined by the colour lacquer application. The more unevenly the colour lacquer is rolled on, the more intensively and vigorously the rust formation imitation. The colour lacquer can also be “dabbed” on to the surface or otherwise accentuated, depending on what the “rust nests” should look like.
- The more colour lacquer is applied, the more intense the rust effect appears in those areas.
- An especially plastic rust effect is created when the rust colour lacquer is dabbed into the still-wet pigment filling layer in areas. After drying and applying the rust colour lacquer, especially intense “rust nests” form with flowing transitions.
- The type of sanding of the provided filler surface also influences the type of rust formation. The coarser the substrate, the more rustic the structuring of the imitation rust. Additional accentuation can be achieved by unevenly filling the pigment filler with a trowel or other tools. This achieves a much more rough structure.
- By individually coloring pigment fillers and/or the finishing lacquer, special colour effects (e.g. the imitation of different metals) can be achieved.
- Adding the effect booster also gives the surface a more interesting feel. If this effect is not desired, this additive does not have to be added. However, the effect will then be significantly flatter and will not feature as much visual contrast.
- Furthermore, additional effect additives (metallic, structure additives, etc.) can be added to the colour lacquer and/or the following coat of clear lacquer.
- Varnishing with clear lacquer affects the look and feel, but the surface’s resistance is significantly improved.
- The lacquers can, of course, also be applied with a spray gun. In our experience, the effect is better and more “rust-like” if applied with a roller, which is why we recommend it as the most efficient method. This decision depends on local conditions and should therefore be made by the user.
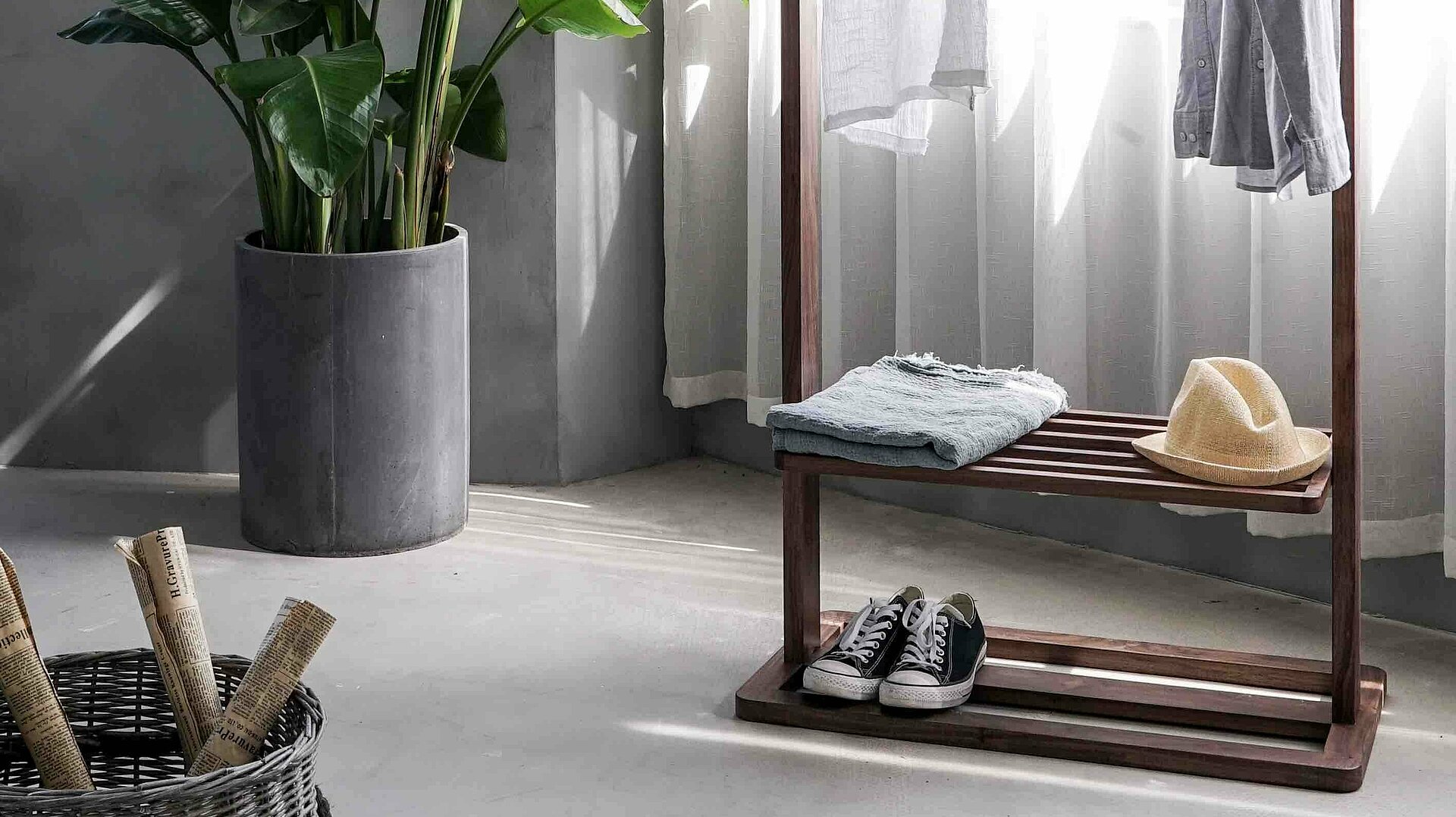
Technical Information HYDRO rust effect
Products required
- When using in damp rooms, please use a HYDRO-PU Insulating filler, e.g. PERFECT-FILL HDP 5650-9343.
- If an especially hard-wearing surface is desired, we recommend an additional coating of PERFECT-TOP HDE 54000, ideally with the addition of 10 % Effect booster HZ 76 in order to maintain the desired look and feel.
- Please follow the precise specifications for hardeners and other optional additive quantities as well as the drying times. Pay attention to careful stirring or mixing in of all necessary components
- To avoid adhesion problems, HYDRO lacquered surfaces should be freshly sanded on the next day before the finish is applied.
- Each prepared surface is a unique piece!
- Please conduct a sample coating under real conditions
Contact partner
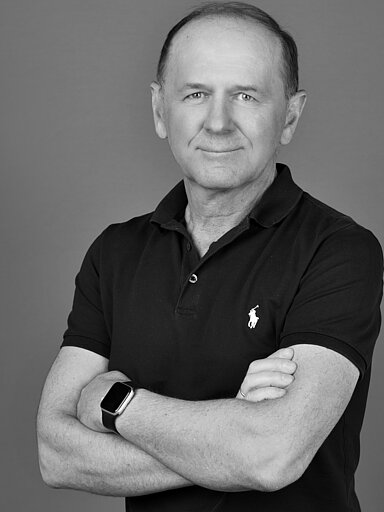