Tips on surface defects
Finding the root cause and rectifying surface defects
Surface defects are always annoying. Here we show you how to avoid defects or how blemishes caused by the coating process can be remedied. You’ll find processing information that can provide rapid assistance.
Please note: There are several possible causes for almost every surface defect. Our recommendations are based on experience and are should be assessed on a case-by-case basis. Application -based suggestions are therefore to be regarded as recommendations and are non-binding.
Please feel free to contact us directly if you need to.
Discolouration
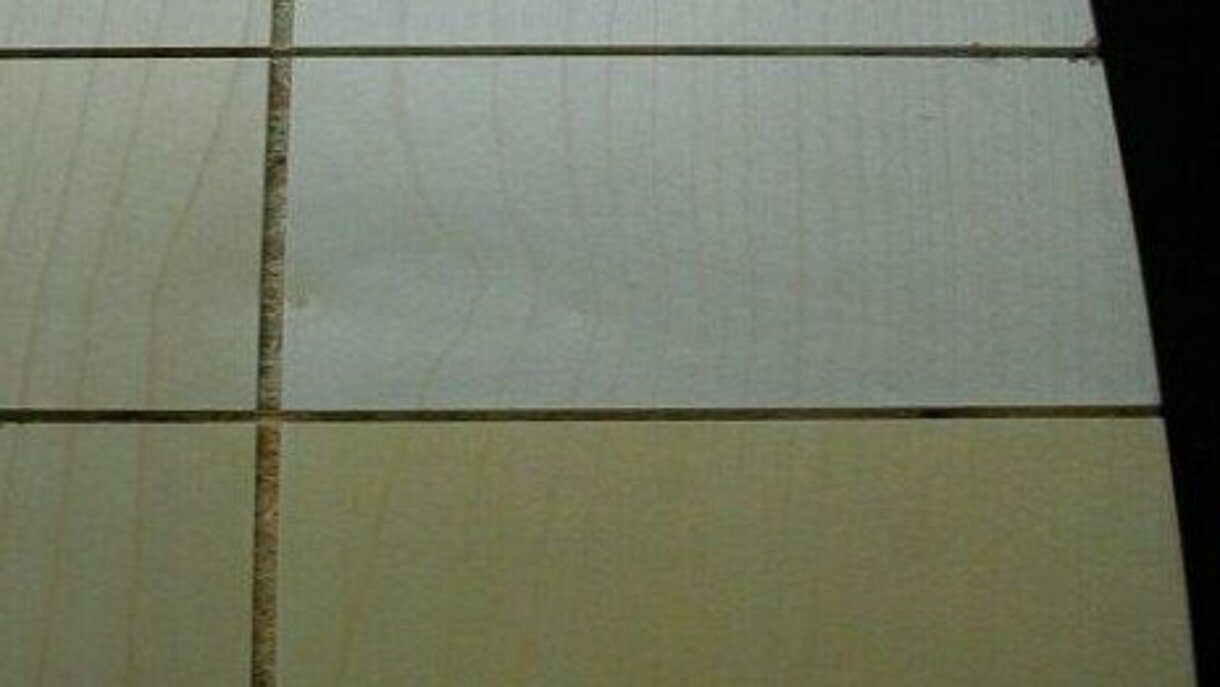
Discolouration
Description of the defect: Brown discolouration of a stained wood surface when using an unsuitable PU system. Reaction between peroxide ( bleaching agent) and isocyanate ( PU hardener ).
Cause of the defect: Using a PU lacquer with a non-peroxide-resistant hardener on a stained wood surface.
Remedy: The discoloured surface can only be recovered by sanding off the layer of lacquer and then recoating with a PU system that contains a peroxide-resistant hardener .
Fogging
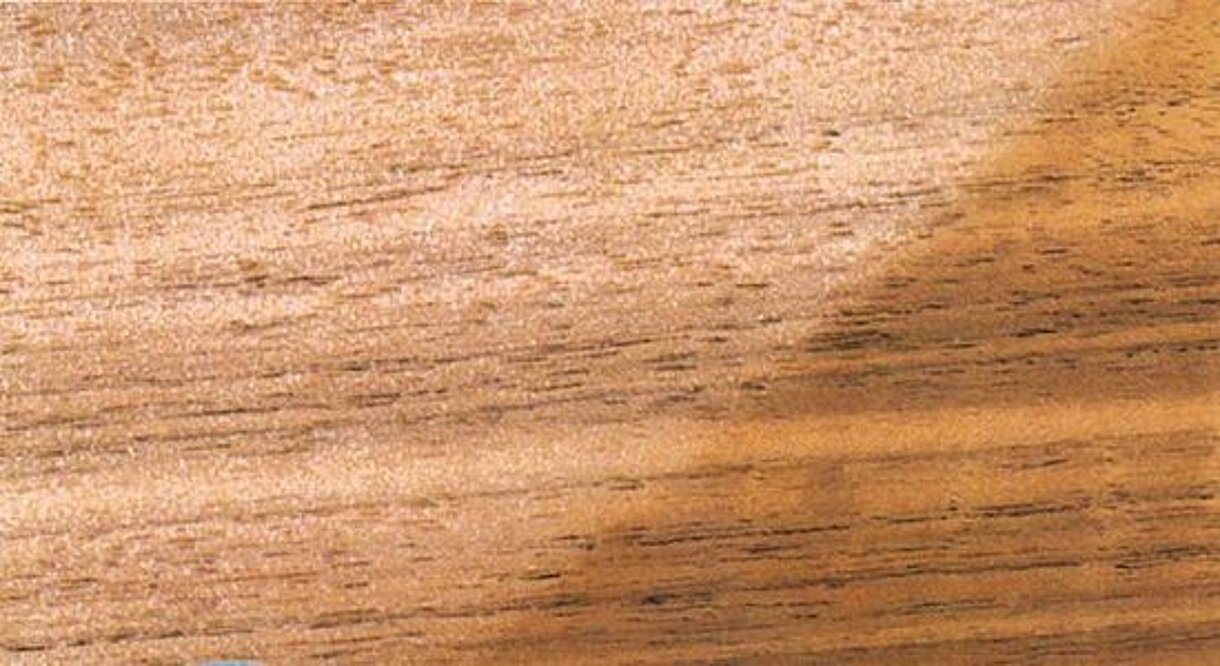
Fogging
Description of the defect: Fogging (white tarnish) is caused by external influences (moisture). These surface defects occur much more in summer given high temperatures and high ambient humidity.
Cause of the defect:
- Excess ambient humidity
- Overly rapid drying of the lacquer material
Remedy: Addition of around 5 % retarder to the coating used.
Yellowing
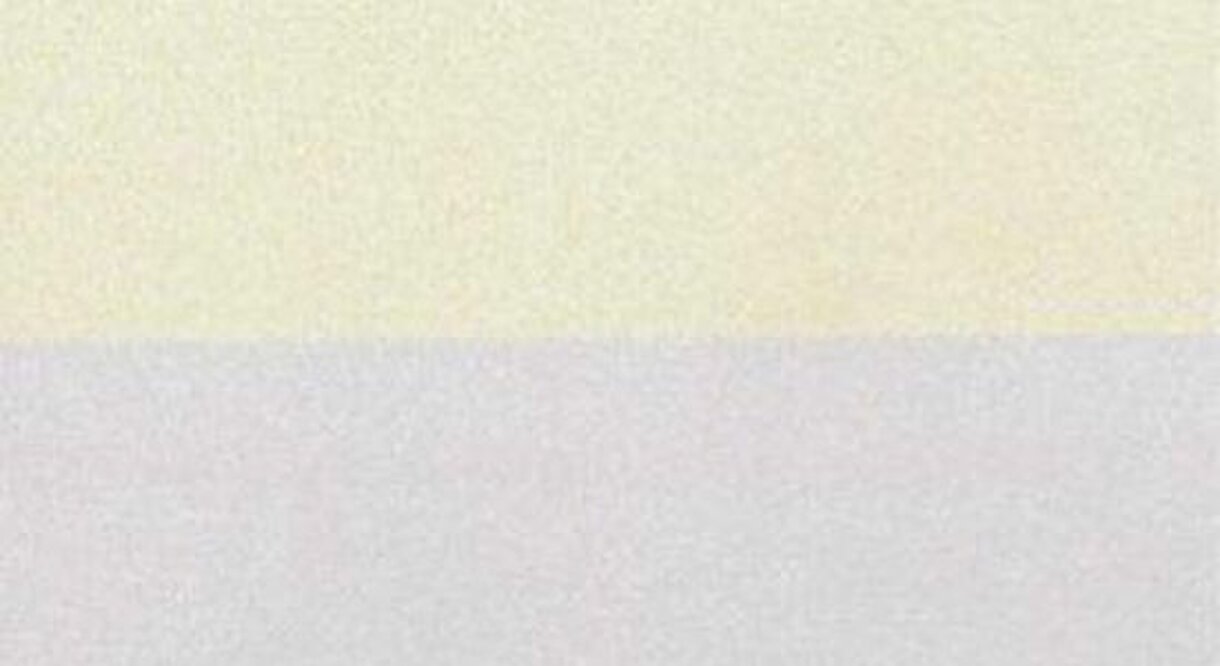
Yellowing
Description of the defect: Change in colour tone of a coated surface
Cause of the defect:
- Use of a CN clear lacquer as finishing lacquer on a light substrate.
- Use of a PU system that isn’t light fast as finishing lacquer on a light substrate.
- Change in the substrate and/or the components that add the colour
Remedy: The yellowed layer of lacquer must be completely removed and replaced with a yellowing-resistant coating. Age-related changes in the wood cannot generally be rectified.
Orange peel
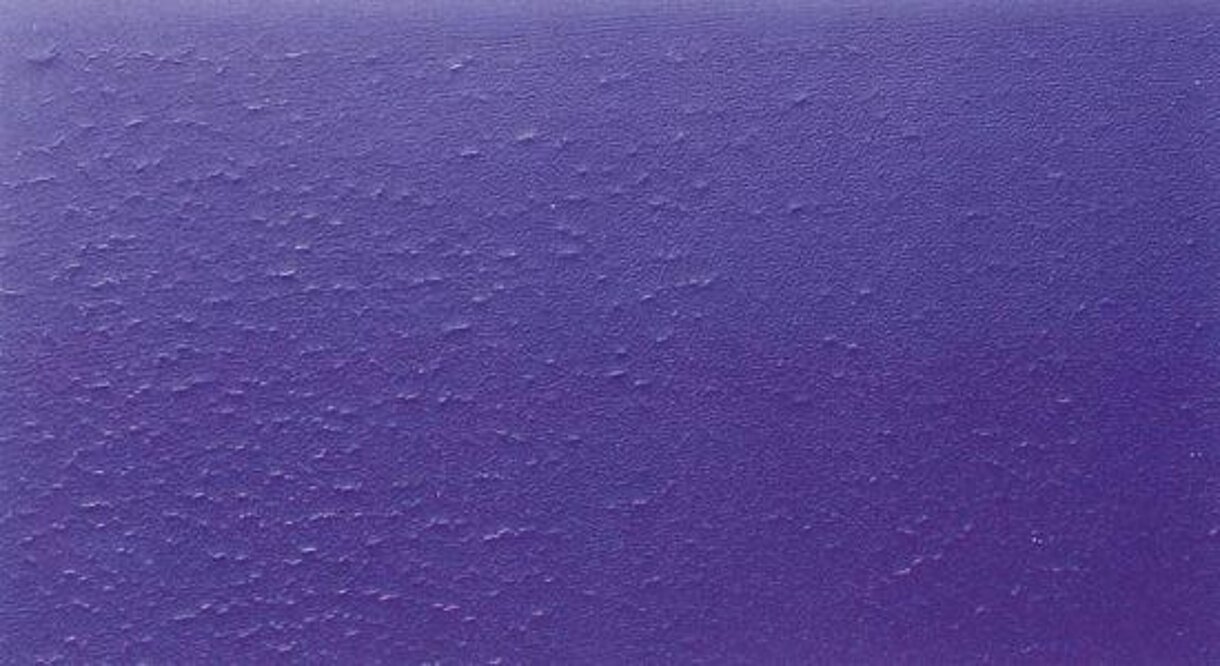
Orange peel
Description of the defect: Orange peel-like defects in the levelling of the lacquer surface.
Cause of the defect:
- Insufficient material applied
- Material too viscous
- Too large a spray nozzle at too low a pressure (poor atomisation)
- Overly rapid drying of the lacquer material (increased room temperature)
Remedy: Sand the defective surface down well at 280 - 320 grit and recoat with the same coating previously used in accordance with the instructions (adding suitable thinner if required).
Crater formation
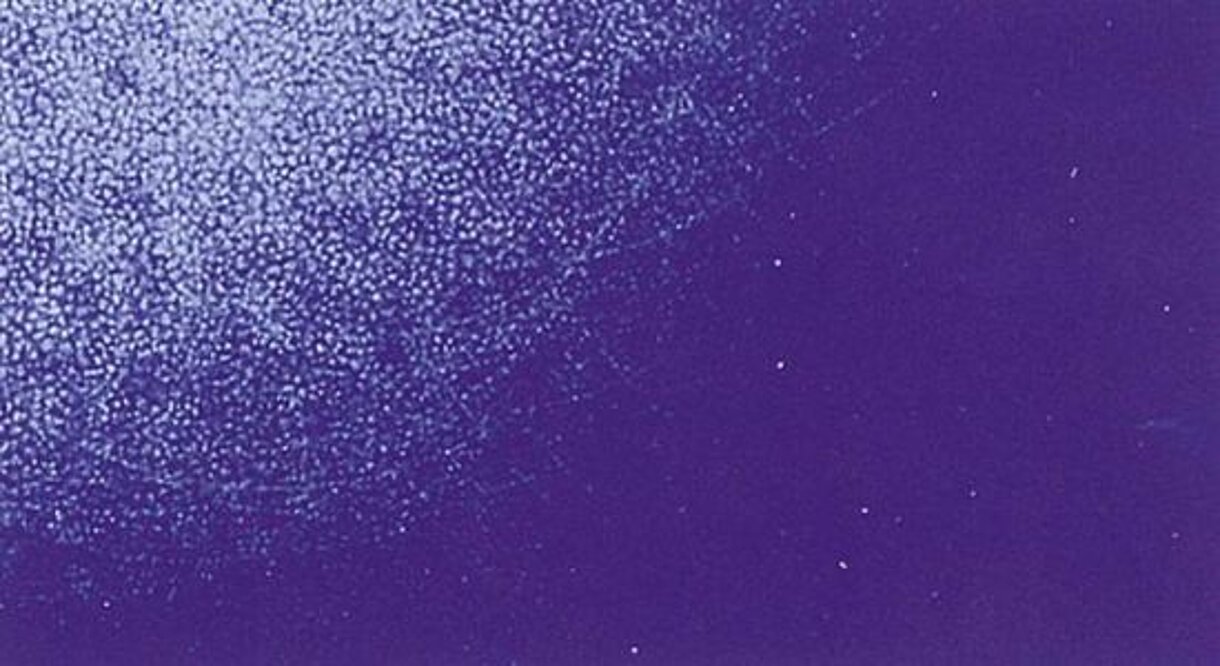
Crater formation
Description of the defect: Irregularly confined wetting defects to the lacquer in the substrate caused by different surface tensions between the lacquer and the substrate .
Cause of the defect:
- Substrate contaminated with oil or grease
- Defective seals in an airless sprayer
- Contact with unsuitable hand creams/rubber gloves/conveyor belts
- Tools or additive containing grease or silicone
- Contamination in the lacquer
Remedy
- The source of the defect must be remedied.
- Where the damage is severe, sand the surface down to the substrate and, if required, reconstruct the surface by adding anti-silicon ZD 385 (ZD 3985).
- Given the formation of slight craters, sand the surface down at 320 grit, apply a very thin mist of the coating used as before and once it has dried for a brief period, finish with 1 x thin coat of suitable lacquer in order to achieve even levelling.
Bubble formation
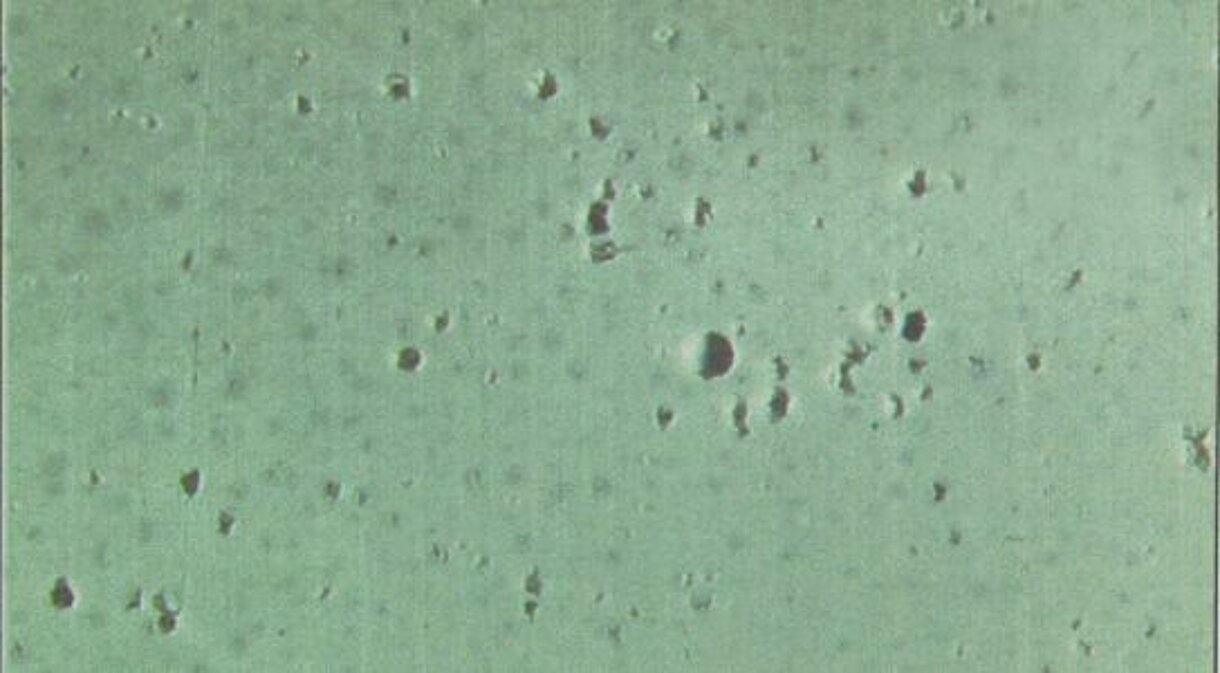
Bubble formation
Description of the defect: Bubbles and trapped air in the lacquer film.
Cause of the defect:
- Overly rapid drying due to excessive temperature or air velocity
- Lacquer material too viscous
- Excessive coat thickness
- Air trapped in the substrate
- Formulation not optimised
- Unsuitable coating material
Remedy: The defective surface needs to be sanded clean with fine sanding paper (280 to 320 grit) until you have a smooth, level surface. Then recoat with 1 - 2 x thin coats of suitable lacquer in line with the processing parameters.
Lifting/ formation or wrinkles
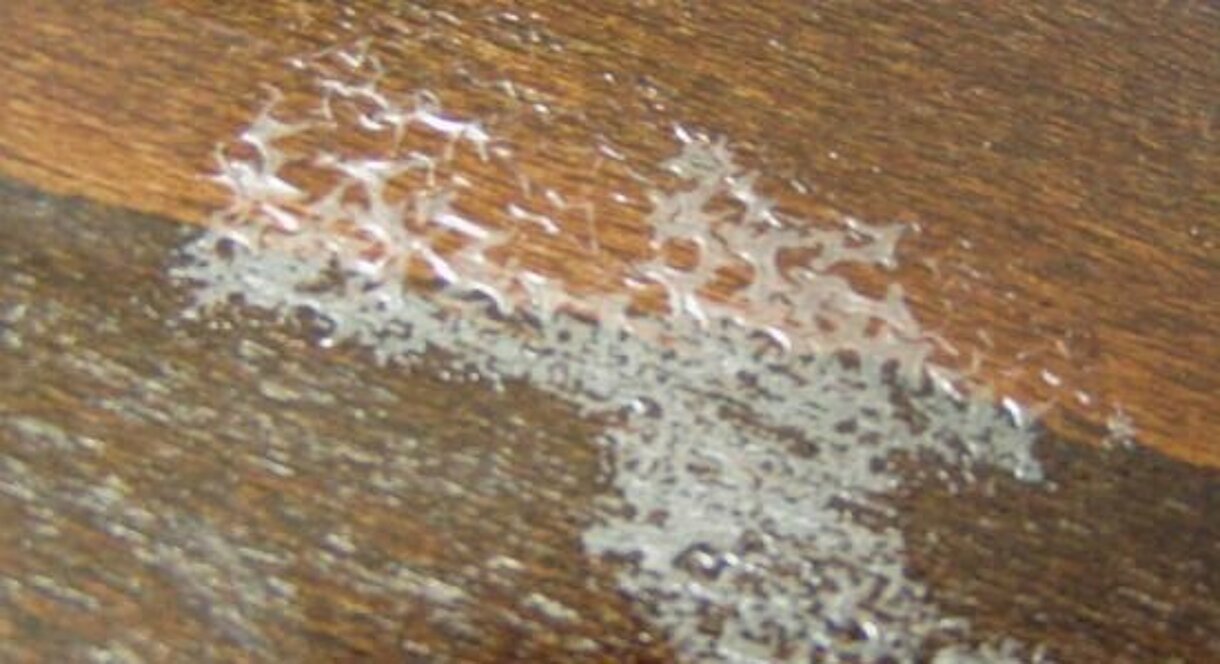
Lifting/ formation or wrinkles
Description of the defect: Crimping or respectively cracks forming in a multi-layer finishing procedure.
Cause of the defect:
- NC Basecoat or unhardened PU Basecoat subsequently recoated with a solvent-fast lacquer system, and after complete hardening a further solvent-based top coat. (The solvent in the top coat diffuses through the solvent-fast (middle) layer of lacquer into the dissolvable coat which swells in size.
- Coats of PU lacquer that are too thick or respectively, processes that follow on from each other too quickly.
Remedy: Identify the cause (surface process, intermediate drying) and then weigh up the options for repair,
- Including removal of the entire damaged lacquer layer and recoating in line with the processing guidelines.
- Sanding the coating well until you have a flat, level surface and then add a mist of heavily diluted lacquer material. When doing so, the lacquer needs to be applied as dry as possible to prevent the solvent from affecting the lacquer surface. In general, this can only be done with smaller workpieces.
- Recoating with a system that doesn’t dissolve into the substrate (water-based lacquer, synthetic resin lacquer, etc.).
Adhesion problems
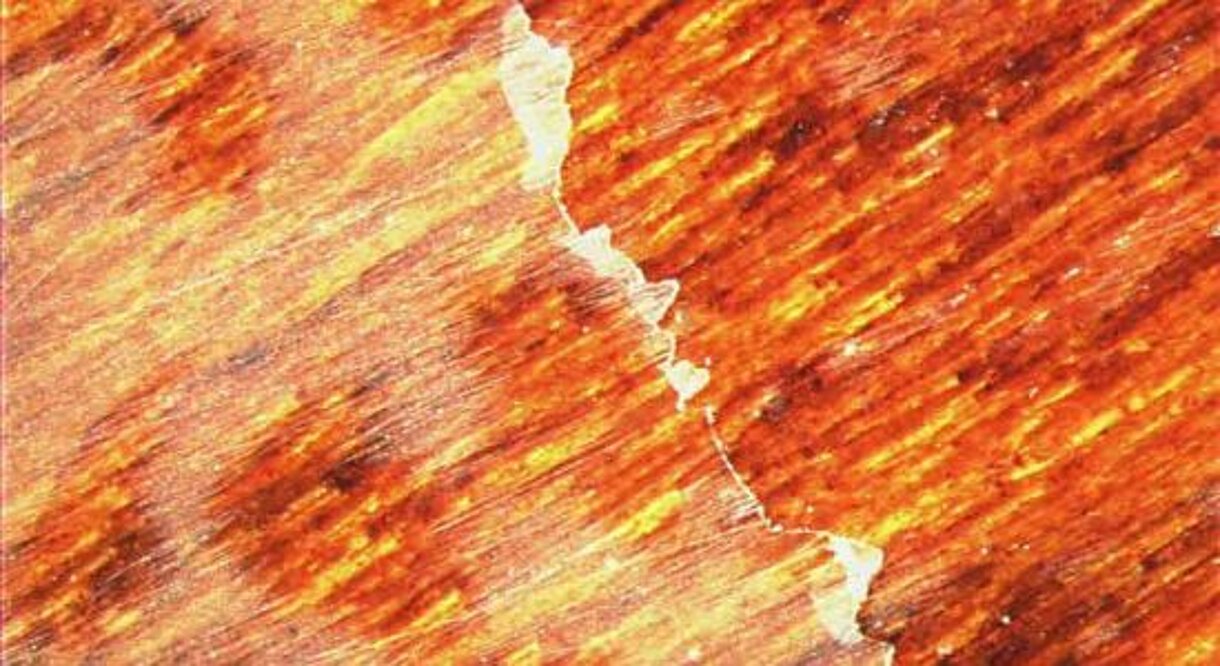
Adhesion problems
Description of the defect: The lacquer layer does not exhibit the required adhesion with the substrate (cross cut test).
Cause of the defect:
- Defective substrate preparation (grease not removed, not properly sanded).
- Unsuitable substrate (contains paraffin or release agent).
- Unsuitable lacquer system.
- Incorrect hardening of the lacquer system
- Basecoat insufficiently sanded
- Sanded basecoat left in storage for too long
Remedy: The poorly adhered lacquer layer should be fully removed. Then pre-treat the surface in accordance with instructions and reapply a suitable lacquer material.
Cell formation
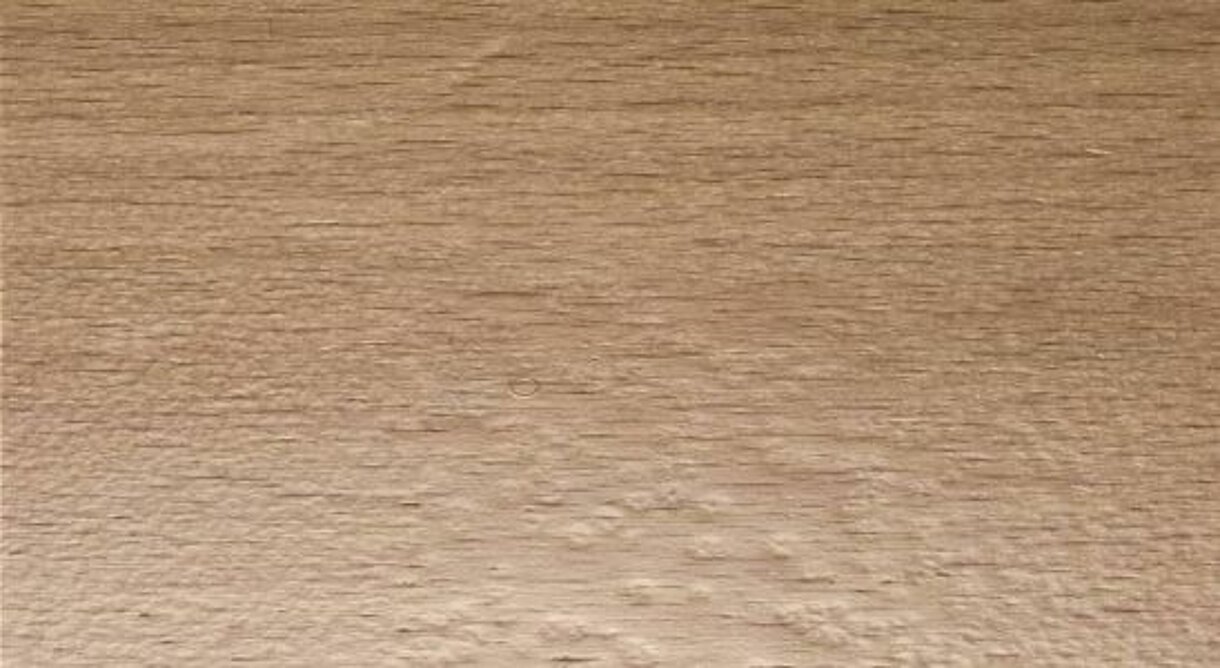
Cell formation
Description of the defect: Bénard cells are visible honeycomb structures in the surface of the lacquer caused by the different flocculation behaviours of the matting and sanding agents.
Cause of the defect:
- Excessive lacquer application in each step
- Lacquer material insufficiently viscous
- Excessive draughts during processing
- Lacquer not ideally suited to the processing
Remedy: Sand the surface down well at 280 - 320 grit. Then recoat with a suitable coating.
Cloud formation
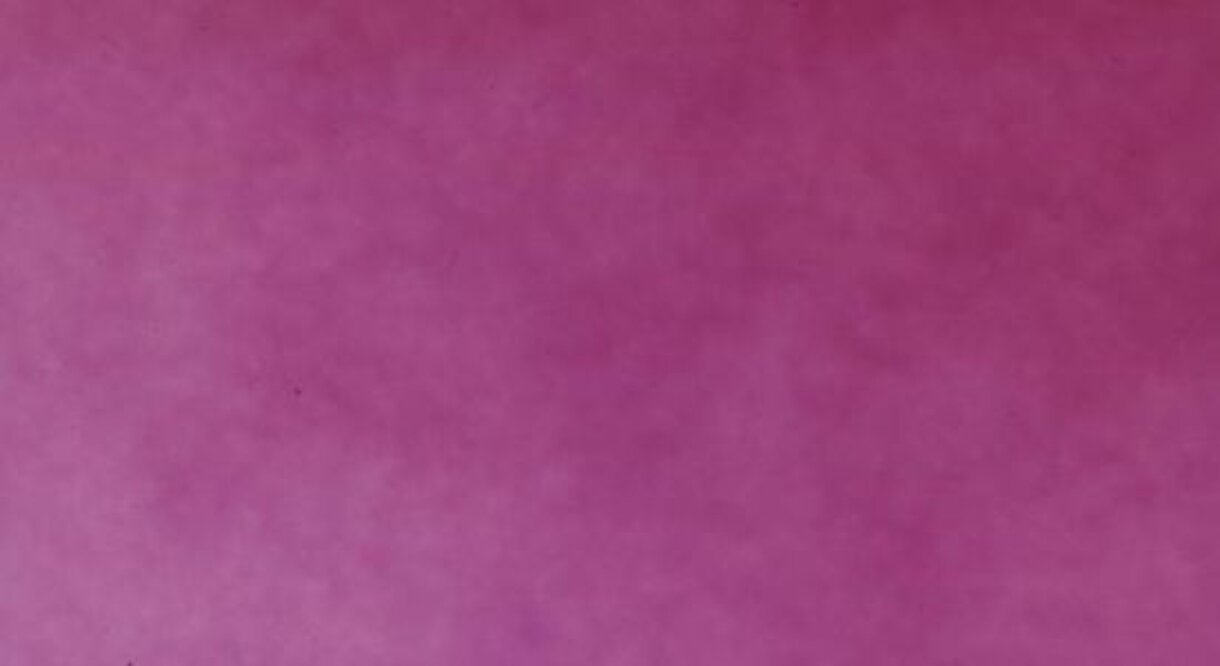
Cloud formation
Description of the defect: Irregular, cloudy matting of the surface due to slight differences in the gloss level .. The lower the gloss level , the darker the substrate and the larger the surface, the more vulnerable the surface during spray application .
Cause of the defect:
- Differing application quantities, excessive coat thickness
- Nozzle too large or defective
- Inadequate pressure, atomising pressure not adapted
- Spraying angle too low
- Altered substrate preparation, i.e. different basecoat, altered complete hardening
Remedy: Sand down and recoat cross-wise with suitable application parameters, if necessary add a second coat with a short intermediate drying period.
Striation
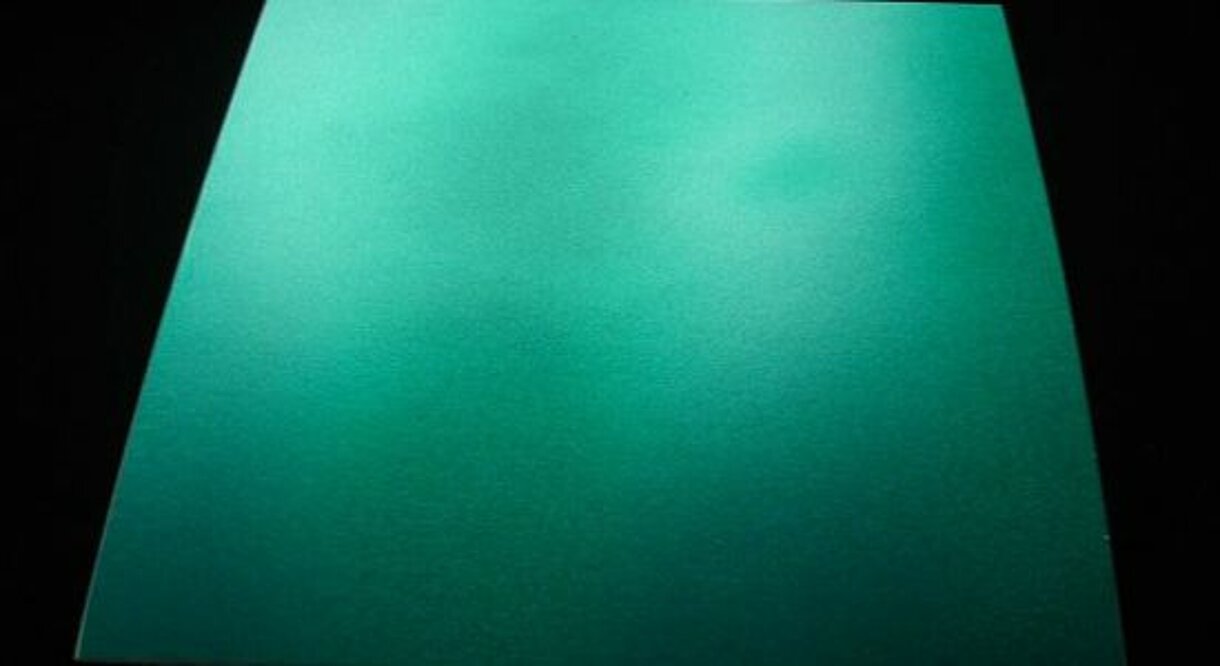
Striation
Description of the defect: Surface with matt striations and/or streaky colour tone.
Cause of the defect:
- Inadequate overlapping when spraying
- Unsuitable nozzle (spraying arc too narrow).
- Blocked nozzles
- Insufficient material applied
- Unsuitable feed rate
Remedy: Sand down and recoat with adjusted spraying parameters.
Formation of cracks
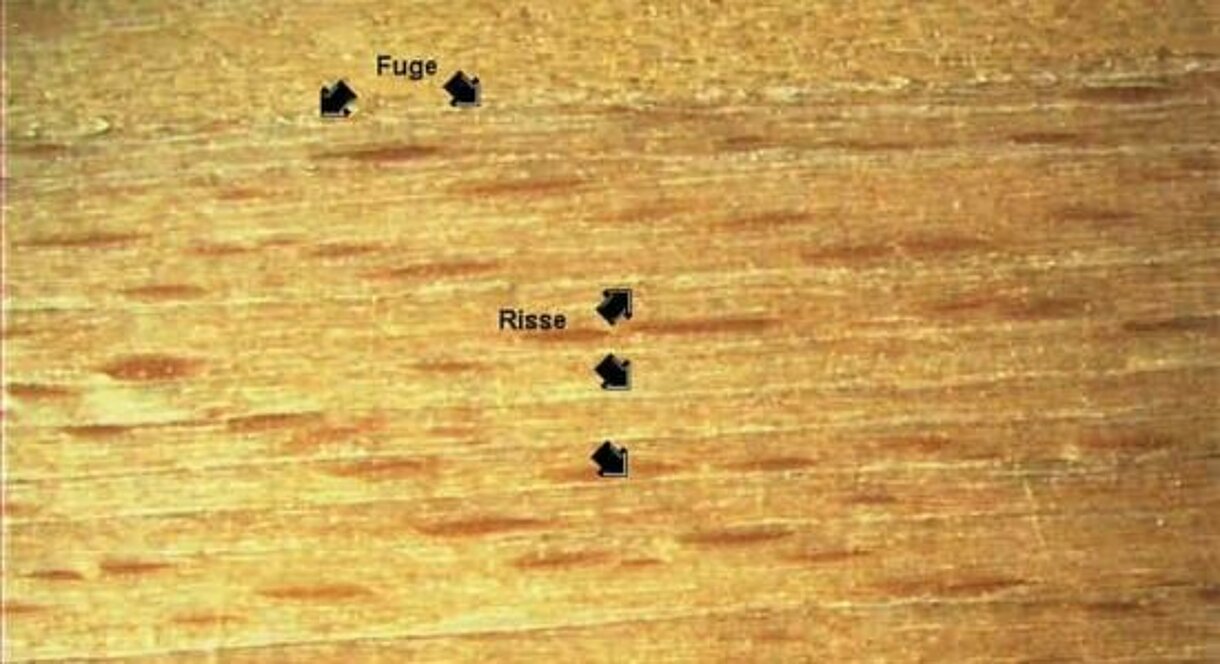
Formation of cracks
Description of the defect: Longitudinal cracks along the pores or web-shaped cracks spread either partially or over the entire surface.
Cause of the defect:
Longitudinal cracks along the pores, mostly cracks in the veneer due to:
- Unsuitable veneer, such as multiplex without over-veneering
- Veneer insufficiently bonded
- Swelling of the veneer/ shrink cracks
Web-shaped cracks, mostly cracks in the lacquer due to:
- Excessive lacquer application, lacquer system too brittle
- In the case of PU lacquers: Hardener omitted
- Lacquer/hardener mixture too old
Cracks in the MDF edge
Remedy: If the cause of crack formation lies with the coating, sand the lacquer down to the bare wood and recoat with a suitable system, otherwise renewed preparation of the object.
Contamination
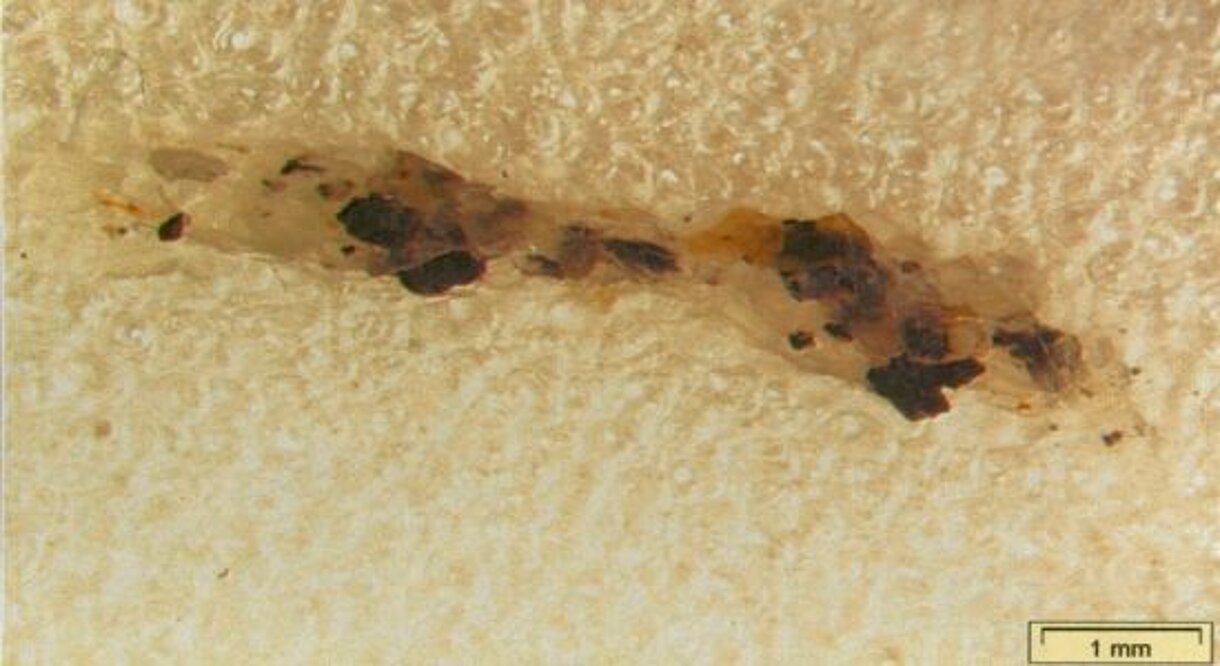
Contamination
Description of the defect: Visible and tactile deposits in the surface.
Cause of the defect:
- Dust incursion
- Overspray
- Contamination in the lacquer
- Unclean tools
- Contaminated lines
- Spray water
Remedy: First check the point of origin/ production area, rectify the cause and remove the source of the defect. Dirt can usually be easily identified with the help of a linen tester. It typically involves irregularly confined particles that may also be thread-like. Air pockets conversely have a regular circular shape.
Gel particles (dried lacquer residue from hoses, guns, etc.) Stippling due to gel particles with air bubbles Contamination of the substrate (beneath the lacquer layer)
Blotching
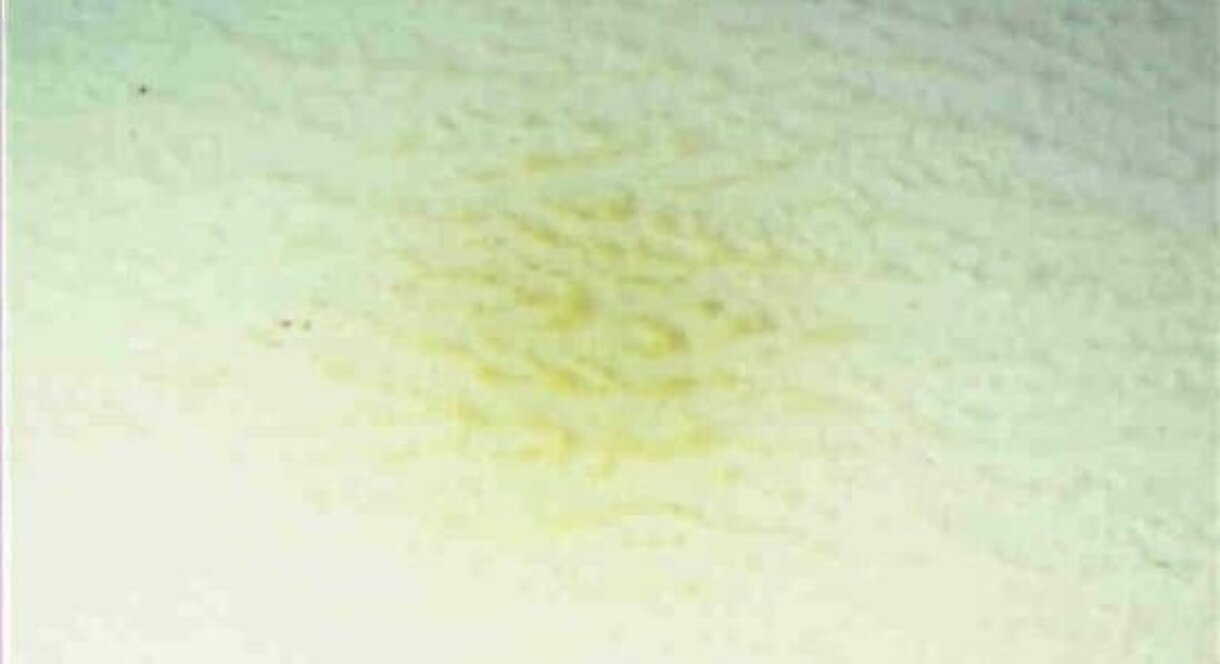
Blotching
Description of the defect: Blotches or dot-shaped discolourations of the surface finish with even or uneven shapes that are uniformly or non-uniformly distributed on the surface.
Cause of the defect: There are various possible causes, here are some examples:
- Brownish blotches can be caused by the reaction of a CN lacquer with certain substances (amino-compounds) in specific UV coatings
- Release from rubber compounds (for instance rubber feet/protectors on telephones, Hi-Fi equipment, vases, ashtrays, etc.)
- Contamination by assembly foam residues (these are colourless at first and only turn yellowish-brown over the course of time)
- Wood that is rich in tannin (e.g. oak) or wood that has water-soluble wood contents (such as ash) can suffer from colour change when coated with Hydro lacquers
- Remains of iron or other rusting metals in the wood (such as metallic sandpaper residue) can cause black spots when combined with water (such as when using Hydro stains or lacquers)
Remedy: A discoloured surface can only be recovered by completely sanding off the layer of lacquer and then re-coating with a PU system.
If the blotches/ discolourations are directly on or in the wood, these must first be removed by suitable means (sanding, washing, etc.) before a renewed attempt at applying a top coat.
Technical Hotline
for individual support
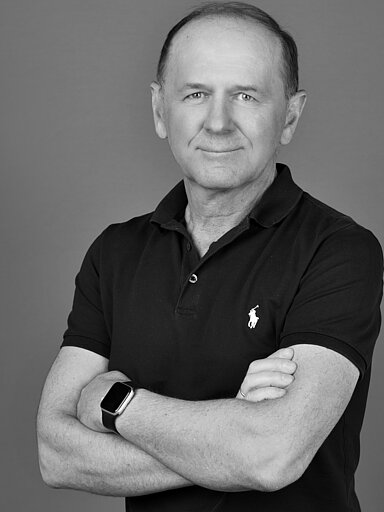