Your benefits
When using Oxi-Reactive-Oil for Roller Coating
Over 90 % renewable raw materials
Sustainability doesn’t come any faster or more efficient than this!
Use your coating line to oil highly sustainable surfaces in 6 min. The market is crying out for natural surfaces and industry requires efficiency.
You’ll find both paired in our Oxi-Reactive Oil for roller coating, which is ideal for use on a coating line to oil furniture, doors or parquet flooring in both coloured and colourless versions. This natural oil is rapidly activated using UV radiation and your parts are immediately stackable. This obviates the need for storage space to enable drying processes. Such brief cycle times would be unthinkable using traditional oxidatively drying oils.
Our rapid oil for roller coating provides highly durable and long-lasting protection with particular scratch resistance that can’t be achieved with a coat of traditional oil. Our Oxi-Reactive Oil for roller coating is certified according to ÖNORM C 2380, precisely because it contains over 90 % renewable raw materials.
Properties of the different oils
All positive features combined
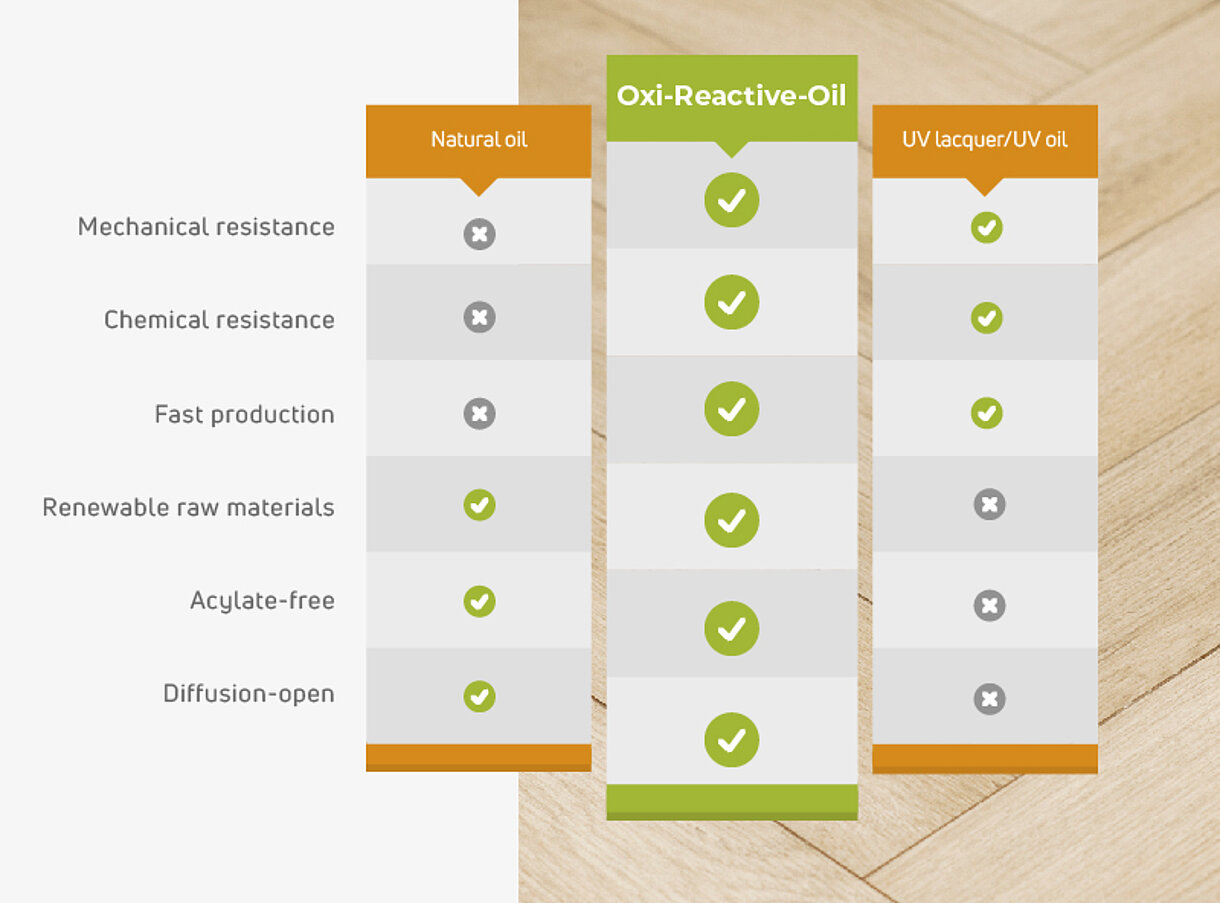
Properties of the different oils
All positive features combined
This overview clearly shows the many advantages of our Oxi-Reactive Oil for roller coating. It exhibits good chemical and mechanical resistance, is acrylate-free, diffusive, consists of over 90 % renewable raw materials and surface protection is possible at record speed.
Traditional natural oils or the UV oils frequently used in industry cannot combine these advantages.
Conventional oils vs. Oxi-Reactive Oil
Cycle time 24 h vs. 6 min
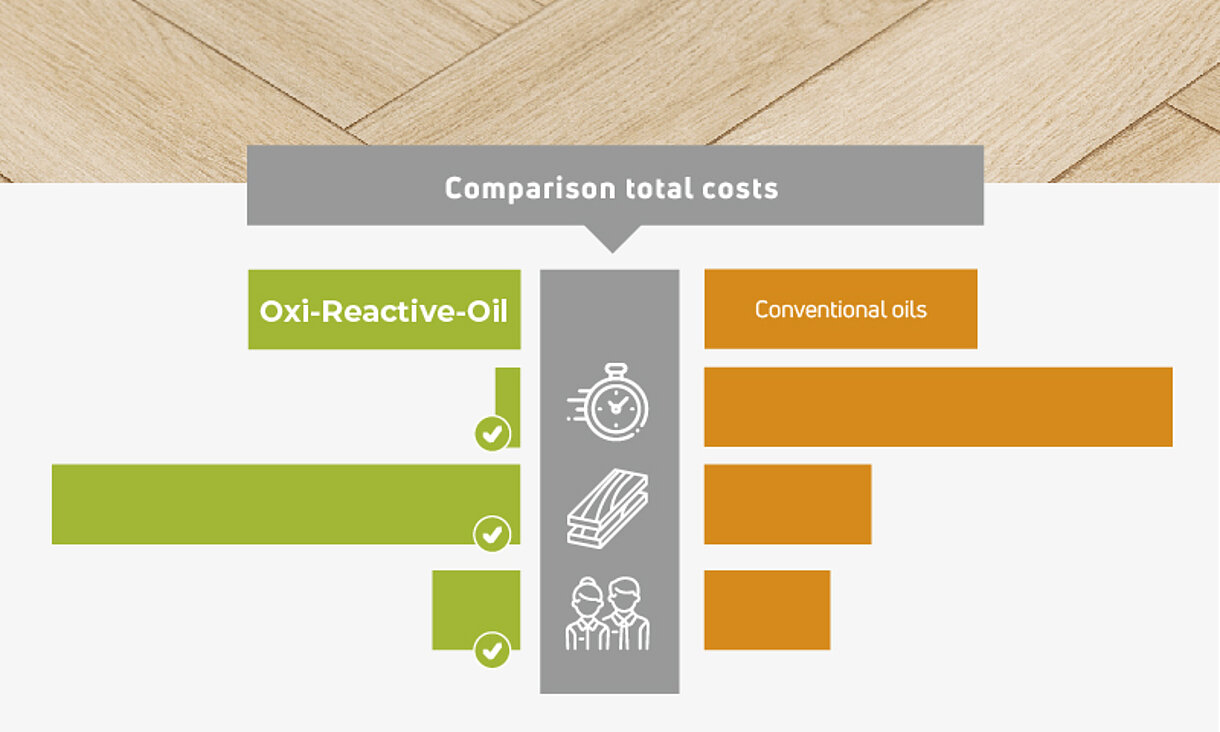
Conventional oils vs. Oxi-Reactive Oil
Cycle time 24 h vs. 6 min
If you oil traditionally, in the best case you have a cycle time of 24 h. The biggest time wasters are the long drying times between oil applications and especially the length of time for complete drying prior to packaging.
The attractive alternative in terms of time is our Oxi-Reactive-Oil for Roller Coating. This gives you an average production time for multi-colour oil application of 10 min including packaging. Drying time is eliminated because UV activation takes place after each oil application and the surfaces therefore dry as quickly as possible.
All in all you save a vast amount of space, time and personnel resources!
Short layout offers space gain
A practical system plan
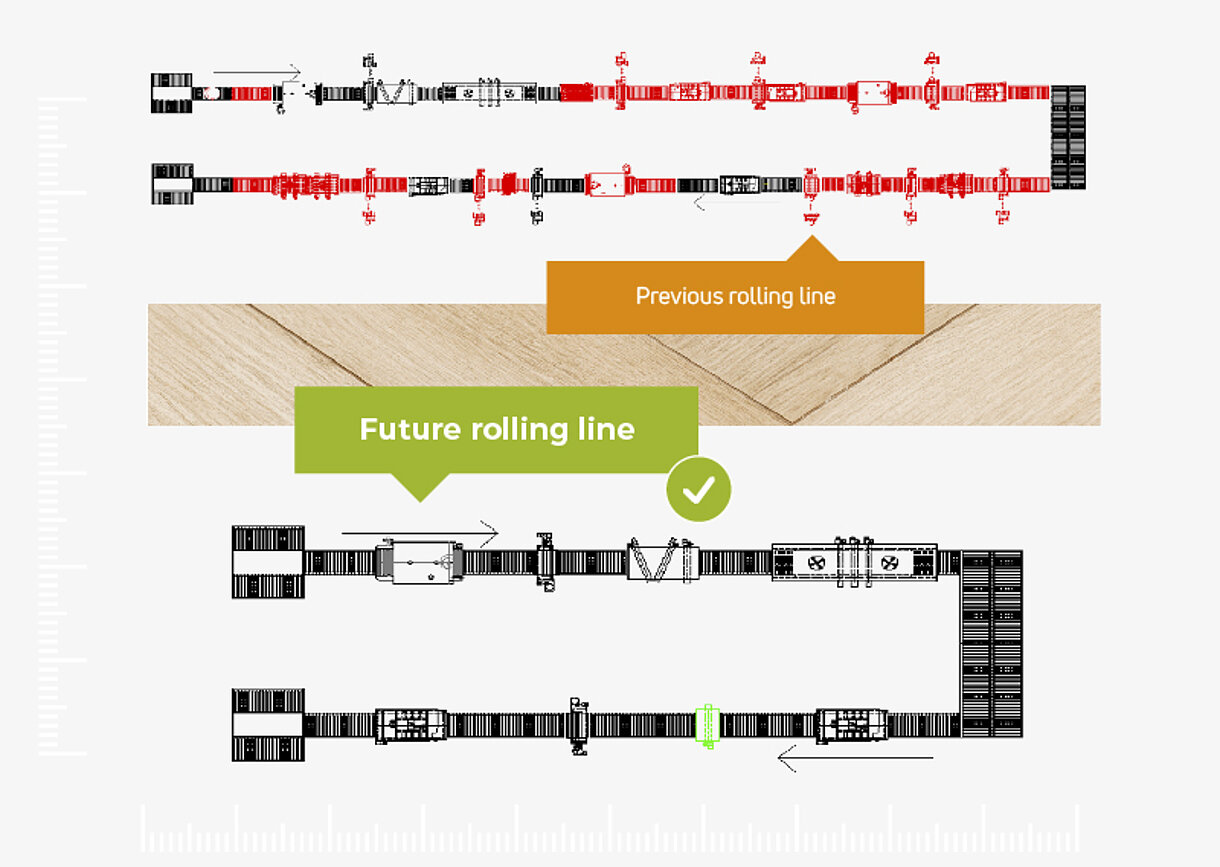
Short layout offers space gain
A practical system plan
Your future rolling line that uses our Oxi-Reactive Oil for roller coating could look like this:
Feeder -Sander -Base oil roller -Distributor station -IR dryer (optional) -Angular transfer -UV lamp -Scotch Brite station -Top oil roller -UV lamp -Stacking unit
These stations are usually already component parts of conventional UV or oil rolling lines. Alternatively you could shorten your existing route, or add a Scotch Brite Station as necessary. The space saved by eliminating trolleys for drying is immense! Make effective use of this saved space for other things.
Would you be interested in our system consultancy? Contact us.
Contact partner
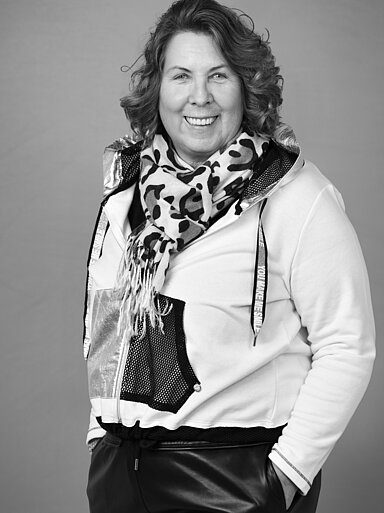
Kwidzinski-Kleine
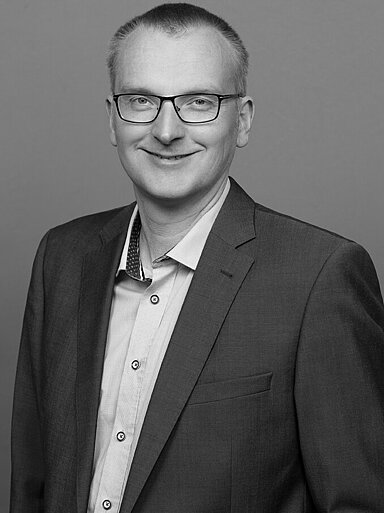